Ваз 2109 заводская шумоизоляция: Заводская шумоизоляция в багажник на ВАЗ 2108,2109,2114 за 990 руб. в интернет-магазине
Шумоизоляция салона ВАЗ 2108 2109 и 21099 » ВАЗ 2108, 2109, 21099, 2113, 2114 и 2115. Тюнинг, ремонт, переделка, статьи и многое другое. ВАЗ 21081, 21083, 21083i, 21091, 21093, 21093i
«Погремушка», «Торохтелкова скрипелка»… Такие и другие похожие прозвища носят модели ВАЗ 2108-99 за то, что даже в новой машине все детали салона скрипят и гремят довольно сильно, особенно если машина с высокой приборной панелью (ВП). Мой автомобиль не был исключением, поэтому через какое-то время эксплуатации я понял, что так больше не могу. Нужно было что-то делать — и я принялся искать подходящее решение этой Проблемы (с большой буквы «П»)
Хочешь сделать хорошо — сделай это сам
Почитав отчеты про Иваново, решил — обязательно поеду, только выберу время (это был февраль 1999). Но потом узнал о возможности заказать готовый комплект и установить его самому. Уверенность в поездке пошатнулась… Тем более что обозначился фронт работ по электрике:
- провода для акустики
- установка эл.
замков в задние двери
- установка ЭСП
- освещение багажника
- доп. стоп-сигнал (нормальная инсталляция)
- замена ЧЯ старого образца на новый
- ремонт проводки боковых электрозеркал
- подключение доп. датчиков (уровня тосола, омыв. жидкости…)
- и еще сигнализацию хотел привести в порядок.
Имело смысл сделать все это заодно с шумоизоляцией (ШИ). Потом в конференции появился VadimAB, я записался к нему одним из первых. До меня они сделали три машины, из них одна 2109. Вариант заманчивый — никуда ехать не надо, ребята ставят ШИ, а я разбираюсь с электрикой. Но… Ничего плохого говорить про Вадима не буду (его и так ругают в конференциях), только я приехал, посмотрел на них и на процесс работы и отказался.
И решил все делать как обычно, т.е. самому. В общем-то решение было единственным изначально — такой объем работ по электрике за день не сделаешь. Следующий вопрос — материалы.
«Динамат» отверг сразу: дорого.
Сказано-сделано, согласовал все эл. почте, после недельной переписки окончательная смета была готова. Привожу ее в полном виде, цены по состоянию на 26.03.99:
Всего получилось порядка $130 за почти двойной комплект. Вопрос с пересылкой решился сам собой — у них была оказия в Москву.
Названия материалов требует расшифровки. Приведу лишь краткое описание, подробные характеристики можно найти на сайте СТП.
Вибропласт
Основной вибропоглощающий материал, который я использовал при обработке металлических поверхностей. Очень похож на лист замазки (напоминающей строительную или герлен), раскатанный по фольге средней толщины.
Особенности:
Считается, что при оклейке вибропластом нагревать поверхности не нужно. Не согласен! Вернее, поклеить-то можно, но на самом деле пятно контакта не будет 100%, особенно если фольга помята. Или нужно работать летом в жару, когда на улице 30+ и материал разогрет на солнце. Я работал при +10С, поэтому грел феном обе поверхности, прикладывал, опять грел и потом разглаживал с применением грубой физической силы. И сам, кстати, при этом грелся 🙂
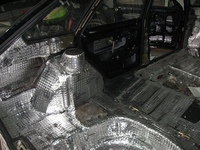
Визомат
Синтетический материал, напоминающий тонкий линолеум, только пожестче, особенно на холоде. Имеет клеевой слой. Мне прислали визомат толщиной 1,5 мм, хотя заказывал двухмиллиметровый. Правда, количеством побольше. Его наклеивал в основном на пластмассовые детали.
Особенности:
На железо клеить 1.5 мм не имеет смысла, только 2 мм. Лучший вариант — это М3 , он 2.5 мм и со слоем фольги. Но я про такой только слышал. Требует очень хорошего разогрева и обезжиривания поверхностей. Значительно хуже вибропласта повторяет сложный рельеф. При нанесении на теплонагруженные участки может «поплыть». Такой пример: под концевик багажника я подложил стопку из 4-х кусочков визомата. Так если подергать за верхний, то все 4 слоя двигаются туда-сюда! В общем, качество клеевого слоя оставляет желать лучшего.
Интересная деталь: на сайте СТП цифровые показатели на визомат есть, а на вибропласт — отсутствуют. Как сравнить эти два материала, какому отдать предпочтение? Спецы СТП утверждают, что коэффициенты вибропоглощения у них приблизительно равны. Но еще до начала работ я попытался опытным путем определить лидера.
На дно кухонной мойки с обратной стороны поочередно наклеил одинаковые куски материалов. И с вибропластом струя воды создавала меньший шум, чем с визоматом.
Битопласт
Отличная вещь, для каждого «зубильщика» просто must have! Представляет собой поролон (бывает разный, но я брал 3 мм ) пропитанный битумом и с клеевым слоем. Идеально подходит для проклейки торпеды и других пластмассовых частей, значительно лучше поролона, т.к. имеет клеевой слой — нарезай да приклеивай, не скрипит, пропитка битумом придает материалу некоторые клеящие свойства, поэтому аккуратно проклеенный козырек торпеды стоит как влитой.
Материалы, расположенные сверху вниз:
Липлен
Битопласт (нарезанные полоски)
Визомат М2
Вибропласт
На разрезе виден СПЛЭН 3004, сверху наклеен Декор.
Пенка без клея — тот же СПЛЭН, но в два раза толще (8 мм)
«Пенка»
Это пенополиуретан, встречается в виде «туристических ковриков», отличный тепло — и шумоизолирующий материал. Не впитывает воду, неплохо тянется. Я брал часть 8мм и 4 мм с клеевым слоем (четырехмиллиметровая пенка идет как СПЛЭН 3004) для вертикальных поверхностей и 8мм без клея для пола.
Декор
Тот же СПЛЭН, только со слоем дерматина 🙂 черного цвета для декоративной отделки багажника и задних арок колес, по внешнему виду немного страшноват, но с другой стороны, у меня в багажнике никто не ездит 🙂
На обработку передка моторного отсека и капота взял готовые комплекты, на передок клеится вибропласт и СПЛЭН 3008, а на капот вибропласт и липлен. При этом на щиток передка куски нормальные, полноразмерные, а на капот — не совсем. ..
Кусочки вибропласта можно было нарезать и побольше. Хотя и с такими, разумеется, эффект есть.
Перед наклейкой липлена все хорошо промовилил и просушил.
Эти фото несколько нарушают очередность этапов — капот обрабатывал в последнюю очередь. Хотя может имеет смысл наклеить комплект ШИ сначала на капот в качестве тренировки.
Инструменты
Прежде всего — строительный фен, без него не обойтись. Для раскройки использовал резак с отламывающимся лезвием и ножницы, которые при резке материалов с клеевым слоем слегка смазывал машинным маслом. Вибропласт и визомат разравнивал скребком для льда, обернутым несколькими слоями сукна. Пробовал приспособить для этой цели узкий валик, но он сразу же сломался 🙂
Начало
Для начала провел тотальную разборку салона, слил тосол, снял печку. Удобный случай как следует ее перебрать. Штатную изоляцию выбрасывать не стал, а вывесил ее сушиться. Влага под ковриками была. Осмотрел все резиновые заглушки в днище, вызывавшие подозрения посадил на мастику.
Установщики не настаивают на снятии печки, я же из салона вынес все.
Начал с передка. Слегка смоченной в ацетоне тряпкой протер железо, наклеил заготовки вибропласта. потом положил второй слой. Хорошо прогревал листы, старался прижать их и разровнять как можно лучше.
Потом оклеил вибропластом все остальное, иногда наносил второй слой. Места для двойного слоя выбирал интуитивно. Дополнительно задемпфировал щиток передка, арки передних колес, тоннель над резонатором, часть заднего сиденья и место под ногами водителя и пассажира.
Обработал мовилем и мастикой незаклеенные участки и стыки на днище, залил антикор в «горбы» под передними сиденьями. Все вентиляционные отверстия в кузове старательно проковырял отверткой и побрызгал в них мовилем.
Похоже на космический корабль, не правда ли?
Арки задних колес не очень удобно оклеивать — сложная форма…
.
На крышу наклеил куски вибропласта в размер между поперечинами. Заодно починил антенну — ее ставили на сервисе… От плафона протянул провода для освещения багажника, бросил провод для дополнительного стоп-сигнала.
С дверями пришлось труднее — в центре уже наклеен кусок «шумоизоляции», который страшно вспучился и местами отвалился. Ситуация осложнялась еще и тем, что сверху эта «ШИ» имеет бумажный слой… В общем, я обработал эту нашлепку железной щеткой как смог и сверху наклеил кусок вибропласта, сильно его нагрев. Остальные участки заклеил визоматом, правда пришлось основательно смыть антикор изнутри — иначе ничего не приклеится. В завершение восстановил антикоррозионное покрытие мовилем и мастикой, смазал замки дверей.
Внутри визомат и вибропласт.
Видно, как установлены электрозамки дверей.
На наружную часть двери наклеил куски визомата, а потом всю поверхность заклеил пенкой СПЛЭН 3004, цельным куском. В передних дверях, где демпфирование обусловлено также и установкой акустики, визомат наклеил на обе поверхности внутренней части двери.
В багажнике место под номером заклеил визоматом, куски вибропласта нанес на внутреннюю часть задних крыльев (если они так называются). Тоже пришлось смывать и потом восстанавливать антикор — на него ничего не клеится.
Пенка
На передок использовал пенку из комплекта, с клеевым слоем. Ее поклеил встык, швы заклеил бумажным скотчем. На крышу прилепил листы 8 мм пенки в размер между поперечинами. Пенку без клеевого слоя крепил на двусторонний скотч, нарезав его небольшими кусочками.
Пенка прекрасно крепится на двусторонний скотч. Его применяют при настилке ковролина.
На пол пенку положил цельным куском, немного внахлест на щиток передка. Под педаль сцепления и газа сделал вырезы.
Для оклейки арок колес и пола багажника использовал «декор». Качество клеевого слоя в этом «сэндвиче» не очень высоко, поэтому местами «декор» отклеивается. Особенно это проявляется на поверхностях сложной формы и в жару. На тот момент я не знал о существовании пластмассовых кожухов для багажника, иначе обязательно интегрировал бы их в свою конструкцию.
Арки задних колес и пол багажника оклеил «декором». Швы заклеил черной изолентой, но со временем она отклеилась.
Хорошие результаты дает сочетание пенки и визомата, наклеенного сверху. Стандартпластовцы рекомендуют применять это сочетание для достижения наибольшего шумопоглощения. Кстати, штатная ШИ выполнена именно по этому принципу, поэтому я и не стал ее выбрасывать. Такую композитную конструкцию я применил позднее, на втором этапе шумоизоляции авто.
Пластмассовые детали
Если даже кое-как поклеить вибропоглощающие материалы, побросать поверх куски пенки, то уже можно наблюдать эффект от проделанного. Но про обработке пластмассовых деталей такой подход неприемлем — «погремушку» нахрапом не возьмешь! Если поставлена цель искоренить все пластмассовые скрипы, то здесь нужна основательность и последовательность. Вдобавок нужно учитывать следующее: при снижении общего уровня шума станут слышны даже те скрипы, о существовании которых ранее сложно было догадаться. Знаете ли, меня иногда напрягает негромкое позвякивание ключей в замке зажигания…
Общие положения
Все пластиковые детали демпфировал визоматом — это устраняет «звонкий» пластмассовый звук при постукивании. Материал наносил иногда по всей площади, иногда только фрагментами. Например, можно наклеить несколько лент шириной 3-4 см по диагонали детали, а можно цельный кусок по центру размером 1/3 площади. Нужно прикидывать также увеличивающийся вес детали и обоснованность тотального покрытия.
На все поверхности, которые соприкасаются либо друг с другом, либо с корпусом авто, наклеивал битопласт. В основном применял полоски шириной 15-20 мм, клеил их вровень с краем (там, где не будет видно, надо сделать с напуском), но также часть деталей заклеивал целиком. Правильно обработанная деталь не должна издавать никаких звуков при интенсивном пошатывании на своем месте.
Обработка пластиковых деталей требует подробного описания, тем более что иллюстраций по некоторым этапам не так много. .. Начну по порядку.
Багажник
Перед началом ШИ у меня были сильные скрипы в обозначенном районе. Когда снял весь пластик, то сразу увидел места, в которых боковые полочки (на которые опирается задняя полка) трутся о кузов в районе штыря, фиксирующего спинку сиденья — в этих местах была потерта краска. На внутреннюю поверхность полок между ребрами жесткости наклеил визомат. Битопласт надо клеить на места соприкосновения с железом и с накладкой задней стойки.
Между ребрами жесткости видны куски визомата.
Динамик и саморезы посажены на герметик.
На краю видна липучка, над динамиком — полоска битопласта.
И вообще освещение багажника очень удобная весчь 🙂
Чтобы свести к минимуму шум от полки, на открывающуюся ее часть приклеил липучку, а остальные места контактов проложил битопластом. Теперь полка практически не трясется. Хотя не мешало бы сзади на нее надеть уплотнитель от ВАЗ 2104.
На саморезы капнул немного Момента, а изолента отклеилась, зараза. ..
Задние ремни безопасности демонтировал, вставляющуюся декоративную накладку приклеил суперклеем.
Спинка заднего сиденья может скрипеть сама по себе, пришлось смазать литолом замки, рычаг и направляющие проволочки; подложить под них полоски битопласта. Все, больше скрипеть вроде как нечему.
Накладки стоек
Всего их 8 штук: две передние, две задние и по две центральные. Передние заклеил визоматом полностью, остальные — полосками по диагонали. Где имеется контакт с металлом или другой пластмассой, наклеил битопласт, в частности возле отверстий под саморезы. Достаточность обработки определял просто: установленные детали не должны хлюпать при постукивании.
Торпедо
Самая ответственная часть. Состоит из козырька, накладки, двух половинок рулевой колонки, накладки воздуховодов, «бороды» и основания.
Основание крепится к кузову в пяти точках — два ушка по бокам, саморез в бардачке и два снизу торпеды — слева и справа. Ушки же часто ломаются; сломалось одно и у меня. Приклеил его там же суперклеем, держится прочно, но все равно пришлось усиливать крепление, т.к. вес торпеды увеличился из-за ШИ.
Есть вариант крепления торпеды к печке саморезами, также вариант укрепления ушек металлом. Верхним краем торпеда входит в резинку лобового стекла; чуть ниже прижимается задней стенкой, но не к щитку передка, а к усиливающей балке (она с отверстиями). Решил привернуть торпеду посередине к этой балке. Для этого на установленной торпеде просверлил отверстия в районе направляющих воздуха на лобовое стекло. Потом притянул конструкцию тремя саморезами длиной 50 мм. Чтобы не сломался пластик, под винты подложил большие шайбы и замазал герметиком.
Если снять накладку воздуховодов, то как раз по центру фото окажутся точки крепления торпеды к балке.
Ту часть торпеды, которая прилегает к кузову, оклеил тонкой пенкой. Нижние участки (полка под бардачком, площади под динамиками и бока) обработал изнутри визоматом и поверх него битопластом. Заодно устранил щели между печкой и воздуховодами, подложив пенку и битопласт.
Крышки воздуховодов не стал оклеивать пенкой изнутри, хотя можно было бы для лучшей теплоизоляции. По всему краю пустил полоску битопласта шириной порядка 15-20мм снаружи и внутри.;
Кое-где виден серый поролон — более ранние попытки провести ШИ. Даже комбинация приборов не избежала обработки битопластом и пенкой 🙂
Кусок сукна местами закреплен двусторонним скотчем — он устраняет шумы от проводки. Because битопласт уже кончился …
На накладку торпеды (металлическую, со слоем чего-то вспененного) ничего не наклеивал. Вполне достаточно битопласта на крышке воздуховодов — при пошатывании на своем месте она не должна издавать скрипов. Кстати, могут скрипеть места соприкосновения ребер, направляющих воздух на лобовое стекло, с накладкой торпеды. В этом случае можно либо наклеить полоску битопласта (можно черную тряпичную изоленту), либо просто смазать места контакта литолом. Особенно такие скрипы могут проявляться при включенной печке, когда все детали нагреваются и расширяются 🙂
Козырек торпеды оклеивал визоматом и полосками битопласта. Очень важно посадить на герметик железные защелки, которые зацепляются за накладку — они постоянно дребезжат…
Металлический кронштейн «конкретно» залит герметиком. И помогло!
Наклеить цельный кусок на верхнюю часть не позволяют ребра жесткости. Для верности сверху положена еще одна полоска.
Если дребезжат кнопки на своих посадочных местах, то их можно укрепить тонкими кусочками замазки, либо нанести немного черного (прозрачного) силиконового герметика. На салазки от приемника тоже наклеил визомат.
Козырек в сборе
Дополнительно укреплять козырек не стал. Однако мысль с уголком хорошая — достойна повторения.
После всех проделанных операций козырек держится как влитой, однако его можно укрепить дополнительно. Про это писал VadimAB в конференции. Делается так:
— снимается левый дефлектор печки
— берется металлический уголок 25Х25 (подойдет от детского конструктора) и крепится одним концом к левой боковине козырька винтом М4(М5) таким образом, чтобы другой конец уголка приходился точно под саморез крепления накладки воздуховодов.
Если после этого установить дефлектор на место, то он закроет собой уголок и винты крепления.
Половинки кожуха рулевой колонки оставил как есть — это чуть ли не единственная (!) деталь в автомобиле, на которую уже нанесена заводская шумоизоляция в виде полиуретановых полосок.
Остальное
«Борода» оклеивается визоматом, по краям полоски битопласта. Самое время подкорректировать форму бороды над педалью газа. Пластмассовые ушки торпеды, к которым крепится верх бороды, у меня отломались. Одно я приклеил суперклеем, а другое потерялось. Поэтому «бороду» пришлось крепить саморезами к ушкам козырька при помощи железных скобок — «гаек» для саморезов. Конечно, это не есть правильно, но и так вся конструкция прекрасно держится и не шатается.
Справа на фото «борода» подрезана таким образом, чтобы нога в зимней обуви не цеплялась за пластик в районе педали газа.
И печка в ноги при этом дует лучше.
Такая тотальная оклейка визоматом необязательна.
Фонарики освещения багажника можно разместить в этой детали.
Дефлекторы
Центральное сопло в печке не заклеивал — использую его летом в качестве вентиляции, да и зимой при прогреве машины частенько открываю. Поэтому пенкой заклеил только левую половину сопла в печке, а соответствующую половину центрального дефлектора зафиксировал суперклеем. В правой половине смазал литолом все точки крепления лопастей. Боковые дефлекторы тоже смазал, а чтобы они не скрипели и не вываливались из своих мест, обернул их черной тряпочной изолентой (только китайского производства — в ней больше клея!)
«Обработанные» дефлекторы прекрасно держатся на своих местах, не скрипят и при необходимости легко демонтируются
И это оказалось очень удачно — от тепла изоленту размякла и дефлекторы прочно зафиксировались на своих местах. Кстати, я довольно высоко оцениваю эту изоленту как прокладочный материал, если кто-то не сможет найти битопласт, то его можно заменить изолентой.
Крышку «перчаточного ящика» оклеил визоматом изнутри, защелку смазал литолом. Внутренность выклеил ковролином, использовав полоски двустороннего скотча. Теперь в «бардачок» можно бросить что угодно и не ожидать громыхания на всех ухабах!
Накладку тоннеля пола тоже оклеил визоматом, на участок перед рычагом КПП наклеил прямоугольный кусок ковролина. Воздуховод выкинул, сопло заглушил куском поролона, но не целиком. Оставил щель шириной порядка 15мм для того, чтобы воздух попадал в тоннель. Теплый тоннель в холодную погоду добавляет в авто еще немного уюта …
Сборка
Всю штатную ШИ разложил по местам, закрепил скотчем провода, проходящие по полу. Отчищенный ковер расстелил по полу, прикрутил все пластмассовые накладки саморезами, установил сиденья. Некоторые трудности возникли при установке тоннеля пола на место из-за бОльшей толщины покрытия. Также пришлось немного подрегулировать педали — подрезал пенку под педалями газа и сцепления.
Должен отметить, что салон довольно безболезненно перенес увеличение толщины покрытия — в конце концов все стало на свои места. Только передние кресла двигаются вперед-назад с бОльшим усилием, немного цепляются за поднявшийся ковер.
Оценка результатов
На чудеса и волшебное превращения «зубила» в BMW конечно же не рассчитывал. Много в машине и таких мест, которые не удается изолировать. Например, уплотнители дверей и стекол — конструкция устаревшая, отлично пропускают шум, особенно на высокой скорости.
Первое, что поразило при первой поездке после ШИ, так это «проглатывание» трещин и мелких ухабов. Кузов намного лучше гасит удары и вибрацию, машина не вздрагивает целиком от малейшей трещины на дороге. Наверное, похожие ощущения должны быть от «проваренного кузова».
Вдобавок намного меньше стала ощущаться скорость. Раньше при скорости 120км/ч я начинал чувствовать, что еду быстрее обычного… Теперь же со скорости 90 и до 160 практически нет разницы, ну разве только ветер за окном шумит посильнее.
Второе — это салон. Торпедо НЕ СКРИПИТ и НЕ ГРОМЫХАЕТ, а багажник ведет себя как будто у меня седан 🙂 И если что-то гремит сзади, то это только вещи в багажнике!
Шум от двигателя тоже уменьшился, но не так как хотелось бы. Причину я выяснил и ликвидировал, но уже на втором этапе ШИ. Коробка стала потише, шум от дороги также заметно снизился. Хотя если на дороге плохой асфальт (с крупным гравием), то такой шум пробивает все заслоны насквозь …
Двери закрываются намного тише и глуше, вот если бы еще и замок переделать… Например на «Фелиции» точно такая конструкция замка, отличие лишь в том, что часть деталей пластиковые. А закрывается он просто неслышно! Были в конференции всякие способы борьбы с замком, но это все не выход…
Крыша теперь просто железная, капли дождя слышно только на заднем стекле — оно не триплекс. Особой разницы после обработка капота не ощутил, ну да ладно, время остывания двигателя проверю зимой.
Так как вместе с ШИ приводил в порядок печку, то она стала греть лучше. Да и вообще, в салоне по субъективному восприятию, стало как-то уютнее…
Никаких замеров по шуму я не проводил, но думаю, что минимум три децибелы удалось снять. Сравнить могу только с «Фелицией». По уровню шума моя машина явно приблизилась к ней, а вот по уровню «вздрагивания кузова» думаю, даже будет получше. Но главное не это — намного комфортнее стало ездить в автомобиле. Мой брат (как сторонний наблюдатель) утверждает что «…это совсем другая машина». Где-то я с ним согласен, может просто отношусь более скептически к своей работе. Но уж чего нельзя не заметить, так это трамвайные пути. Теперь переезд через них на скорости 60 км/ч не напоминает землетрясение в 7 баллов по шкале Рихтера, пережитое в трамвае, а воспринимается как кратковременное неудобство…
Минусы
Даже не знаю что сказать… Так как все делал сам, то каких либо глюков не было по определению. Попутно с ШИ починил все что требовалось и остался очень доволен этим фактом. Единственное, что можно отнести к отрицательным моментам, так это увеличения веса авто где-то на 25-30 кг. Да и двери потяжелели — не стоит долго держать их открытыми.
Вот вроде и все… В целом результатом доволен, ничуть не жалею о проделанной работе. Хотя и проглядывает в моих действиях некоторый максимализм: больно достали меня заводские default-установки. С зубилом по-другому просто нельзя — в инструкции ведь сказано: «…после сборки обработать напильником» 🙂 Только пропарился со всем этим я довольно долго, сколько — не скажу, не буду расстраивать…
Обсудить шумоизоляцию на нашем форуме
< Предыдущая | Следующая > |
---|
Шумоизоляция Ваз 2109 — Autodrom.Info
Многие тюнеры почему-то не записывают в список своих достижений шумоизоляцию автомобиля. Однако если ездить на отечественном автомобиле без дополнительной шумоизоляции, то удовольствия от поездки испытать точно не получится.
Не рекомендуется устанавливать сабвуфер на авто без «шумки», потому что мощные волны, которые испускает аудиосистема, будет громыхать обшивкой салона, так что толку от басов мало, когда все кругом трещит и свистит.
Попробуем сделать шумоизоляцию Ваз 2109 своими силами. Во время выполнения работы нам понадобятся следующие материалы: 14 листов материала под названием вибропласт, обезжириватель, крепкий нож, промышленный фен и набор отверток.
В первую очередь полностью разбираем салон Ваз 2109. Удаляем обшивку крыши и дверей, все пластиковые накладки и т.п. Работать нужно аккуратно, дабы не поломать пистоны крепления. В любом случае, не помешает купить дополнительные крепления, благо стоят они совсем недорого.
За обшивкой можно увидеть тонкий слой материала, который выполняет роль звукоизоляции. Днище Ваз 2109 мы трогать не будем, потому что заводская «шумка» там выполнена вполне пристойно.
Следующий этап — обработка металлических частей обезжиривателем. Больше всего внимания уделяем тем местам, куда мы будем крепить новый шумоизоляционный материал. Пришло время приклеивать материал на свое место. Имейте в виду — чем толще шумоизоляция, тем меньше звуков будет проникать в салон. Вырезаем вибропласт кусками, снимаем с него защитный слой и начинаем все клеить.
Наружную панель двери Ваз 2109 лучше всего обклеить полностью, в результате должен получиться закрытый объем. Делается это для того, чтобы обеспечить качественное звучание динамиков в двери. Кстати, для них нужно заранее оставить отверстия соответствующего диаметра.
С крышей все предельно просто, здесь у нас практически ровная поверхность. Приклеиваем материал, крепим обшивку и на этом все. Накладываем вибропласт под панель приборов, на металлическую перегородку, отделяющую салон от моторного отсека.
Остается шумоизолировать багажный отсек. Здесь работать крайне сложно, потому что отсек имеет непростую форму. Придется немного потрудиться и сделать на изоляционном материале надрезы по диагонали. Делаем мы так для лучшего сцепления вибропласта с округлостями. Стараемся не повредить краску в багажнике, в противном случае получим очаг коррозии в труднодоступном месте.
Крепим материал на внутренние и внешние боковины, а также к средней и задней стойкам. Боковые полости можно оставить нетронутыми, потому что динамики туда устанавливаться не будут. Всю поверхность хорошенько разогреваем промышленным феном, разглаживаем так, чтобы не осталось ни складок, ни морщин. Ждем пару часов, пока материал окончательно приклеится, потом начинаем собирать салон «девятки».
Положительный эффект шумоизоляции должен проявиться сразу, стоит завести двигатель и немного прокатиться по неровностям. Если стуки все же проникают в салон, то стоит отремонтировать ходовую автомобиля, но это уже другая тема.
Источник
Шумоизоляция ВАЗ. Как сделать шумоизоляцию капота ВАЗ 2110 своими руками
Многие автовладельцы со временем задаются вопросом, зачем же нужна шумоизоляция капота ВАЗ 2110 и можно ли ее осуществить своими руками не прибегая к помощи специализированный СТО. Отвечая на этот вопрос, хочется отметить, что шумоизоляция капота является одним из этапов общей защиты автомобиля от выбро, звуко, и тепловых волн. Однако оклеив специальным материалом не только внутреннюю часть капота ВАЗ 2110, но и поверхность моторного щита, можно получить неплохой результат, который позволит уменьшить проходимость шумов создаваемых силовым агрегатом автомобиля.
А теперь подробно о том, как сделать шумоизоляцию капота ВАЗ 2110 своими руками. Завод-изготовитель устанавливает между ребрами жесткости внутренней части капота изоляцию, которая состоит из простого синтетичного материала со слоем поролона. Такая защита подходит только для минимального удерживания тепла исходящего от двигателя в зимний период. Перед началом выполнения работ по шумоизоляции капота ВАЗ 2110 необходимо отсоединить клипсы, с помощью которых крепится заводская шумоизоляция, а затем снять ее.
Для шумоизоляции капота ВАЗ 2110 вам понадобится:
ЭКО-4 и СПЛЕН 8 — 1,5 листа.(Размер одного листа: 0,5м х 0,75м, Вес одного листа ЭКО-4: 2,44Кг.)
Первый слой шумоизоляции капота ВАЗ 2110, как правило, должен состоять из вибропоглощающего материала. Для этих целей многие используют вибропоглощающие, демпфирующие самоклеющиеся пластины ЭКО-4 (вибродемпфер), которые изготовлены на основе полимерно-битумной и каучуковой композиции, один из слоев содержит тисненную алюминиевую фольгу. Так как в моторном отсеке создается высокая температура, материал должен при монтаже подвергаться нагреванию с помощью фена, после чего разогретым слоем крепится к металлическим поверхностям капота. В противном случаем при нагревании он может отслоится
Клеим шумоизоляцию на капот ВАЗ 2110 своими руками
Из картона изготавливаем шаблоны необходимых для оклейки внутренних частей капота, после чего по ним вырезаем нужные нам элементы из ЭКО-4.
Перед оклейкой тщательно обезжириваем, метал в местах соприкосновения с виброматериалом. Нагреваем производственным феном, приклеиваем и с помощью валика прижимаем и выравниваем нанесенные части вибродемпфера.
После оклейки выброизоляции таким же образом вырезаем и крепим на внутренней части капота поверх вибродемпфера слой звукоизоляционного материала, к примеру, СПЛЕН 8.
СПЛЕН 8 является отличным звукопоглощающим вспененным пенополиэтиленом, который имеет клеевый слой высокой адгезии. Этот материал обеспечивает звукозатухание, путем перехода колебательной энергии в тепло, за счет трения в звукопоглотителе.
После оклейки СПЛЕН 8 крепим обратно заводскую шумоизоляцию капота и устанавливаем клипсы ее крепления. Как правило, после снятия клипсы приходят в негодность, следовательно рекомондуется заранее прибрести новые клипсы крепления заводской шумоизоляции под капот ВАЗ 2110.
Шумоизоляция ВАЗ 2110 своими руками (видео): материалы, технология проклейки
Print this article Font size 16
Штатная шумоизоляция, которая предусмотрена для ВАЗ 2110, оставляет желать лучшего. Нет, ее нельзя назвать ужасной, но всегда есть к чему стремиться.
Если вам не нравится уровень тишины внутри салона собственной десятки, то есть вы вполне можете решить данную проблему своими силами, проведя шумоизоляцию.
Подготовка к шумке
Основные сложности
Если вы уже разбирали салон машины, то могли заметить, что в ВАЗ 2110 это делается достаточно просто. Даже если вы новичок в этом деле, опираясь на руководство по эксплуатации, работа будет проведена достаточно быстро. Дополнительно советуем опираться на видео уроки. В них можно подчеркнуть много полезного и важного.
Основной сложностью при разборке салона, без которой полноценную шумоизоляцию провести не удастся, является демонтаж приборной панели.
Разбирая приборную панель, обязательно выставляйте метки по всем деталям, иначе обратная сборка превратится в настоящее испытание.
В том же руководстве по эксплуатации есть рекомендации относительно демонтажа приборной панели, потому опирайтесь на нее. Ни в коем случае не выдергивайте все шнуры, а то проблем потом не оберетесь.
Истории наших читателей
“Гребаный таз. “
Всем привет! Меня зовут Михаил, сейчас расскажу историю о том, как мне удалось обменять двенашку на камри 2010г. Все началось с того, что меня стали дико раздражать поломки двенашки, вроде ничего серьезного не ломалось, но по мелочи, блин, столько всего, что реально начинало бесить. Тут и зародилась идея о том, что пора менять машину на иномарку. Выбор пал на таёту камри десятых годов.
Как и любой другой процесс шумоизоляции автомобиля нужно начинать с разборки. Для начала откручиваем жабо, дворники, затем снимаем заводскую шумоизоляцию, а потом и пластиковую стенку за которой находится фильтр салона (для машин до 2003г.в.). Кстати, удобно сразу доработать установку фильтра салона, что я и сделал
Примеры и фото шумоизоляции авто.
В нашем портфолио на сайте опубликовано более 100 работ, где мы пошагово рассказываем, как работали с конкретным автомобилем. Качественные фотографии и комментарии подтвердят наш профессионализм. Убедитесь сами!
всеAudi BMW Chery Chevrolet Datsun Ford Geely Great Wall Haval Hawtai Honda Hyundai Infiniti Jeep KIA Lada Lexus LIFAN Mazda Mitsubishi Nissan Peugeot Renault Skoda Subaru Suzuki Tagaz Toyota Volkswagen УАЗ
все2 Series 2114 3 6 Accord Allion Almera Arkana ASX Auris Aveo BB Boliger Camry XV40 Camry XV55 Camry XV70 Caravelle Ceed Ceratto Corolla E150 Corolla E170 Corolla E180 Cr-V 2 Cr-V 4 Cr-V 5 Creta CX-5 Duster Elantra Emgrand Expert Fielder Fit Fit Shuttle Focus Forester SH Forester SJ Funcargo Fusion Fx-35 Fx37 Golf Grand Cherokee Grand Vitara Granta GS GX H5 H6 Highlander Hover i30 i40 IX35 Jade K5 Kalina Kaptur Karoq Kuga Lacetti Lancer Land Cruiser Largus LC Prado 120 LC Prado 150 Leaf Logan LX Montero Multivan Murano Z51 Murano Z52 Niva Note NX Octavia Odyssey On-do Optima Outback Outlander GF Outlander GT Outlander XL Pajero Pajero Sport Passat B8 Patriot Patriot Pickup Pilot Polo Mk5 Polo Mk6 Priora Prius Probox Q3 Q5 Qashqai J10 Qashqai J11 Ractis Rapid Rav4 XA30 Rav4 XA40 RAV4 XA50 Rio FB Rio JB Rio QB Rio QB Hatchback Rio X-Line RX Sandero Santa Fe Solano Solaris Sonata Sorento Sorento Prime Sportage Stepwgn Superb Tager Tahoe Teana Teramont Terrano Tiggo Tiguan Tiida Toureg Tucson Tundra Vesta Vitara X-Ray X-Trail T30 X-Trail T31 X-Trail T32 X5 X60 XV Х70
Найдено вариантов: 232
Полная шумоизоляция
Уровень КОМФОРТ
Полная шумоизоляция
Уровень КОМФОРТ
Полная шумоизоляция
Уровень ПРЕМИУМ
Полная шумоизоляция
Уровень ПРЕМИУМ
Полная шумоизоляция
Уровень ПРЕМИУМ
Полная шумоизоляция
Уровень ПРЕМИУМ
Полная шумоизоляция
Уровень ЭКСТРА
Полная шумоизоляция
Уровень ЭКСТРА
Полная шумоизоляция
Уровень ЭКСТРА
Полная шумоизоляция
Уровень ЭКСТРА
Полная шумоизоляция
Уровень ПРЕМИУМ
Полная шумоизоляция
Уровень КОМФОРТ
Полная шумоизоляция
Уровень ЭКСТРА
Полная шумоизоляция
Уровень КОМФОРТ
Полная шумоизоляция
Уровень ЭКСТРА
Полная шумоизоляция
Уровень ЭКСТРА
Хотите так же?
Отправьте заявку
на установку
Наш менеджер поможет подобрать
подходящий уровень шумоизоляции,
оценит работу и запишет
на удобное время.
Гарантия бережного
отношения к вашему
автомобилю
Всего 1 день
занимает
комплекс
работ по
установке
Бессрочная гарантия
на комплекс услуг
Другие примеры работ
Уровень Премиум
Уровень Комфорт
Уровень Экстра
Уровень Премиум
Обратите внимание!
Как правильно утеплить дверь автомобиля своими руками. Этапы и особенности правильной шумоизоляции дверей автомобиля Чем приклеить шумоизоляцию на дверь
Полотно дороги, по которому эксплуатируется автомобиль, далеко не всегда качественное. Вкупе с тем, что автопроизводители редко уделяют должное внимание качественной шумоизоляции дверей, частые поездки с плохих поверхностей приводят к расшатыванию креплений кузова, багажника, капота и дверей. О наличии проблем водитель узнает только на второй год эксплуатации автомобиля, если он изначально был куплен новым.Именно двери дают о себе знать в первую очередь. Как осуществляется шумоизоляция дверей автомобиля и какие материалы для этого нужны?
Звукоизоляционные функции дверей
Работы по звукоизоляции необходимо проводить сразу после покупки автомобиля, даже если он новый. Улучшения будут следующие:
- значительное повышение комфорта вождения и снижение риска аварий, при этом посторонние шумы раздражают водителя и делают поездку небезопасной;
- повышены акустические возможности салона, повышено качество звука, устранены вибрации и дребезжание при езде;
- снижаются потери тепла, что приводит к длительному сохранению необходимой температуры воздуха даже при выключенном двигателе.
Выбор материалов
Основным назначением вибропоглощающих материалов является снижение корпусного шума, вызванного вибрацией металлических частей автомобиля (элементов подвески, трансмиссии, двигателя). При выборе конкретного материала необходимо ориентироваться на коэффициент механических потерь. Он должен быть как можно выше. За счет клеевой основы рассматриваемые материалы быстро монтируются и обладают дополнительными герметизирующими свойствами для антикоррозионной защиты металлических элементов кузова.Основой для изготовления представленных ниже материалов является мастика или битум, возможно добавление алюминиевой фольги, но есть и варианты без нее.
- Бимасты представлены в двух слоях — битумном и мастичном. Толщина 2 — 4 мм, внешнее покрытие может быть из алюминия, бумаги или ткани.
- Визомат – вибропоглощающий материал на битумной основе, изготовленный на клеевой основе. Поглощение вибрации обеспечивается комбинацией битума и вспененного полимера.Серия MP отличается наличием фольгированного покрытия.
- Вибропласт характеризуется высокими показателями упругости и гибкости. Структура представлена алюминиевой фольгой, полимерной и самоклеящейся подложкой.
Звукопоглощающие и звукоизоляционные материалы, в свою очередь звукоизолирующие, изготавливаются на основе полиэтилена. Относится к категории дополнительных материалов, используемых после виброизоляторов.
Технологически правильное выполнение работ по шумоизоляции в районе ворот требует подготовки следующих материалов и инструментов:
- шумо и виброизоляторы;
- сшивающий валик;
- растворитель;
- ножницы или строительный нож;
- Фен строительный или бытовой;
- Набор отверток.
Подготовительный этап требует выполнения следующих работ:
- Дверь в разобранном виде открывается. Облицовку необходимо снимать в хорошо освещенном помещении, процесс монотонный и длительный. Старайтесь не повредить крепления и помните о процессе разборки. Механизм стеклоподъёмника не требует демонтажа.
- Второй подготовительный этап требует снятия заводской изоляции и защиты от коррозии.
- На завершающем этапе чистый металл, полученный после демонтажа, необходимо обезжирить.
Поэтапная шумоизоляция в зависимости от степени
Поэтапная шумоизоляция дверей автомобиля своими руками напрямую зависит от степени звукоизоляции, которую необходимо добиться.
Минимальная шумоизоляция
Это бюджетный вариант и не подходит для улучшения акустики, но снижает шум. Обработка двери минимальна и предполагает наклейку вибропоглощающего материала на наружное полотно двери сплошным слоем или не менее 70%.Допускается использование виброгасителя толщиной 2 мм. Для отражения шума также необходимо обработать внутреннюю панель дверной карты; для этого можно использовать шумоизоляционный материал. Дополнительно эта мера послужит защитой от влаги и пыли.
Плоские места карты двери можно подрезать.
Средняя шумоизоляция
Оптимальный баланс между качеством и ценой достигается при средней звукоизоляции. В этом случае специальных материалов больше, да и принцип монтажа несколько иной.Шум со стороны дороги значительно снижается, а в двери можно установить акустику, от которой можно будет получить хорошую отдачу. Порядок действий здесь будет следующим:
- Первый слой — 2мм виброизолятор. В области напротив динамика можно использовать толщину 3 мм и добавить акустическую линзу. Сверху можно наклеить звукоизоляционный материал, но этот шаг необязателен.
- Очистите наружную панель жестким виброгасителем и закройте все технологические отверстия.
- Тонкий вибропоглотитель (2 мм) подходит для обработки дверных карт.
- Для отделки всей внутренней поверхности используется звукопоглотитель толщиной 5 или 10 мм.
Максимальная шумоизоляция
Рассмотренный уровень звукоизоляции будет уместен при необходимости установки в дверных проемах мощной акустической системы с мидбасом. Двери должны быть тщательно подготовлены для таких динамиков. Главной целью в данном случае не будет подавление внешних шумов, хотя с этой функцией такая обработка справится на отлично.Особенности монтажа такого утеплителя:
- В качестве первого слоя для обработки наружной панели следует использовать виброизоляционный материал толщиной 3 мм. Не стоит выбирать материал большей толщины, иначе двери станут слишком тяжелыми.
- В качестве второго слоя используйте звукоизоляционный материал со слоем водонепроницаемого клея.
- Подготовьте алюминиевую фольгу с клейкой основой для обработки отверстий во внутренней панели. Сверху фольги накатайте жесткий виброизолирующий материал толщиной 2-3 мм.
- Финишным слоем будет четырех- или пятимиллиметровый звукоизоляционный материал.
- Не забудьте изготовить дверную карту. Сначала приклейте волнистый звукопоглотитель (10 – 15 мм), а поверх него виброизоляцию толщиной 2 мм.
Экстремальная шумоизоляция
Ключевое назначение данного уровня шумоизоляции представлено подготовкой автомобиля перед соревнованиями по звуковому давлению или громкости передней акустики. Для обработки двери в этом случае необходимо использовать максимально толстые материалы, чтобы обеспечить наибольшую эффективность.Слишком велика вероятность перетяжеления дверей, но этот риск при таком тюнинге уже не учитывается. Этапы монтажа такого утеплителя будут следующими:
- На первом этапе происходит усиление двери с помощью алюминиевых полос, наклеенных на наружную панель через небольшие промежутки. Также роль армирующего материала могут выполнять полосы из жесткого виброизоляционного материала.
- На следующем этапе необходимо раскатать между зазорами вибропоглощающий материал толщиной 4 мм.
- Следующий слой представляет собой звукопоглощающий или звукоизоляционный материал на основе латексной пленки или водостойкого клея. Не забудьте закрыть технологические окна алюминиевыми листами или полиэфирной смолой. Верхний слой будет представлен виброизоляцией толщиной 3-4 мм.
- Кусочки виброизоляции также используются для обработки дверной карты, но предварительно необходимо приклеить шумопоглотитель. Его толщина должна быть как можно больше. Площадь покрытия звукопоглотителем напрямую зависит от количества динамиков, установленных в двери.Так как мидбасов может быть несколько, дверная карта закрепляется на железной части двери при помощи сквозных болтов и только потом монтируется акустическая система.
У многих возникает вопрос о правильной оклейке дверей с шумоизоляцией. В интернете полно информации о разных способах, последовательности и необходимых материалах для звукоизоляции дверей. Перечитывая форумы, разные статьи, люди путаются: одни делают так, другие по-другому, на «форме Мазды говорят, что лучше сделать так, потому что у некоторых так получилось и он доволен», «Опель читал дальше на форуме что двери лучше проклеить одной виброй и лепить спленос на обшивку» и т.д.до бесконечности. Эта путаница возникает по следующим причинам: не каждый пользователь того или иного форума является профессионалом в области шумоизоляции, плюс многие даже не понимают сути «как работает шумо- и виброизоляция» в принципе.
Итак, звукоизоляция дверей включает в себя:
2. Шумоизоляция
3. Противоскрипная обработка
4. Оклейка обшивки двери шумопоглотителем.
Начнем с шага 1 — виброизоляция.
Первый слой ВСЕГДА виброизоляция — устанавливаем на наружную стенку двери (ту, что «смотрит» на улицу). На двери достаточно виброизоляции 2мм, т.к. толщина металла двери совсем небольшая. Виброизоляция должна быть плотно приклеена к самому металлу двери, поэтому поверхность двери необходимо предварительно обезжирить, а виброизоляцию прикатать жестким валиком (при низких температурах, нагретых до +17 минимум). Стараемся максимально покрыть виброизоляцией поверхность.
ЖЕСТКИЕ ЛЕНТЫ В ДВЕРИ НЕ ПРИКЛЕИВАТЬ ВИБРОИЗОЛЯЦИЕЙ!!! Хуже не сделаешь — просто переведи материал — толку не будет.
Вот так будет выглядеть результат p1.
или вот так, если у вас открыты технологические отверстия
Переходим к n2. — Шумоизоляция. Хотелось бы немного уточнить, что шумоизоляционные материалы и звукопоглощающие материалы — это 2 разные вещи (так же, как и слова «изолировать» и «поглощать») — на этом мы остановимся подробнее в следующих статьях.Звукоизоляция у него есть еще одно второе свойство — теплоизоляция, в отличие от звукопоглотителя. Задача звукопоглотителя – рассеивать направленную звуковую волну.
Вторым слоем поверх виброизоляции устанавливаем шумоизоляцию. Это может быть Сплен Шумофф П8, или Комфорт6. Шумоизоляция самоклеящаяся, но все же ее желательно прикатать жестким валиком. Не бойтесь, что у вас не будет целого листа звукоизоляции в двери (физически вы его туда не поставите) — главное, чтобы он был аккуратно и покрыт как можно большей поверхности.
Должно выглядеть так:
Затем снова возвращаемся к n1. Виброизоляция. Для достижения максимального эффекта + для достижения качественного звучания динамиков в двери технологические отверстия необходимо закрыть виброизоляцией (НЕ РАЗДЕЛЕННОЙ, а виброизоляцией), т.к. она имеет приличную жесткость, в результате чего ваш дверь можно рассматривать как замкнутое, полое пространство (что необходимо для звучания музыки).
Должно быть так:
Переходим к шагу 3 — обработка против царапин.Что делаем: обматываем все провода и стержни антискрипом Шумофф Битолон 5мм. Стыки наличника с металлом двери также проклеиваем Битолоном; так же обрабатываем битолоном съемные пластиковые части обивки. Не забываем про клипсы — их тоже обрабатываем антискрипом.
Если есть желание и возможность привести двери в максимально улучшенное состояние, то рекомендуем дополнительно установить частичную виброизоляцию на обшивку двери и полностью оклеить сверху звукопоглотителем (не шумоизолятором, НЕ РАЗДЕЛЕННЫМ ) Герметон А15.Это самым положительным образом скажется на звучании музыки, приятности закрывания двери и тишине во время движения.
________________________________________________________________________________
На этом можно закончить и собрать дверь. Полная качественная шумоизоляция двери.
Мы надеемся, что эта статья поможет вам. Не изобретайте велосипед — звоните, спрашивайте, не стесняйтесь задавать любые вопросы.
Как самому обклеить автомобиль шумоизоляцией
Как самому обклеить автомобиль шумоизоляцией — вопрос актуальный для любого владельца вне зависимости от модели и марки автомобиля, в последние годы экономят на шумоизоляции, поэтому он либо очень слаб, либо отсутствует вовсе.
Процесс совсем не сложный, но ведь всем хочется сэкономить, поэтому важно только знать из чего можно сделать шумоизоляцию в машине, иметь необходимые инструменты и читать наши рекомендации и советы, а после что вы справитесь не хуже мастеров этого дела.
Ошибки новичка
Наиболее распространенные ошибки автолюбителей при выполнении шумоизоляции.
С выбором фирмы-подрядчика
Ошибка при выборе мастерской грозит не качественной работой, банальной потерей денег и, как следствие, отсутствием шумоизоляционного эффекта, и самое неприятное, в этом случае, что вы сделаете вывод, что это не дает никакого эффекта
Ваше присутствие в помещении над вашим автомобилем работают мастера
Как правило, мастера не любят, когда клиенты постоянно суют нос в их работу:
- Это мнение большинства мастеров, с которыми я знаком лично.
- Когда кто-то постоянно стоит над твоей душой и заглядывает тебе под руки в процессе работы, даже можно ожидать очень враждебной реакции
- Почти никому не нравится, когда кто-то постоянно спрашивает «скоро все будет готово?» влияет на результат не лучшим образом
Спешка и отсутствие плана
Когда вы очень загорелись выполнением шумоизоляции и сразу же хотите это сделать:
- Начало работы без планирования будет сопряжено с огромной потерей времени и, конечно же, денег.
- Возможно, вам придется ехать несколько раз, чтобы забрать пропавший инструмент.
- Может случиться так, что вам придется переделывать работу заново.
- Звукоизоляция однажды наклеенная, а затем оторванная уже не пригодна для повторного использования — опять потеря денег
- Кроме того, процесс звукоизоляции — дело, требующее много времени и сил, поэтому следует учитывать времени и сил (за час-два у вас это не получится), здесь придется запастись терпением, упорством и трудолюбием, особенно если вы новичок
Неправильный выбор материалов
Это одна из самых распространенных и неприятных ошибок, от незнания как правильно сделать шумоизоляцию в автомобиле:
- Как правило, хорошие, а тем более качественные материалы всегда стоят дорого Деньги.
- Здесь привычка экономить легко приводит к новым тратам.
- Мало того, что они начнут преждевременно отслаиваться, что приведет к коррозии корпуса, так еще и эффект от таких будет слабенький, и опять же можно возразить, что шумоизоляция не работает.
- Кроме того, некачественные материалы могут нанести вред здоровью, они, находясь в салоне, будут отравлять воздух парами, а потом дышать будете и вы, и пассажиры.
Ошибка с выбором уровня шумоизоляции
Когда сначала вы решите, что достаточно просто утеплить машину по минимуму, то вам будет казаться, что надо было сделать лучше, дороже, толще, но это, как правило, проблема очень экономных людей и перфекционистов
Ошибка с выбором места выполнения работ
В интернете полно описаний и фото процесса шумоизоляции своими руками, которые выполняются куда бы они не попали:
- Прямо на улице, возле офиса, на обочине и др.
- Тут проблема будет в том, что не в том месте, где вы будете делать свою шумоизоляцию, вы либо будете крайне неудобно, наступление ночи застанет вас в самый неподходящий момент
- И самое неприятное, что в этом случае у вас обязательно что-то украдут, прямо из рук, вы можете потерять не только инструменты б а также элементы интерьера, мобильные, радио, видеомагнитофон и т.д.
Использование неподходящих инструментов
Давайте разберемся, как сделать шумоизоляцию в автомобиле, если все работы делать только одной отверткой — и машину разобрать, и виброизоляцию закатать, то это будет как минимум сложно, хотя похоже на правду:
- Однако, если вы хотите сделать работу качественно (чтобы потом что-то не отвалилось), без проблем разобрать/собрать машину, то вам понадобятся соответствующие инструменты
Неуверенность в своих силах
- заглушать внешние шумы и улучшать качество звучания музыки
- По собственному опыту скажу, что даже самый примитивный «шум» дверей дает прекрасный эффект, в в салоне музыка начинает играть намного лучше
- При минимальной программе поклейки дверей требуется только один виброизоляционный материал, вибропласт вибропласт «Серебро» или «Золото» Клеить нужно с внутренней стороны двери прямо напротив двери колонна
- Важно проклеить виброизоляционным материалом наибольшую площадь, от этого зависит качество утепления
- Здесь тоже лучше учитывать вес материала, если утяжеляете двери, то со временем она просядет и вам придется заменить петли
- Если у вас мощная аудиосистема и вы хотите улучшить ее звучание, то минимальными проклейками не отделаться.
- Необходим комплексный подход и минимум четыре слоя (фото ниже)
- Первый слой приклеивается на внутреннюю сторону дверей, куда материал приклеивается через специальные отверстия
- Можно опять же использовать вибропласт серебряного класса (или бимастовые бомбы) за динамиком
- А со вторым слоем — на сверху виброизоляционного материала укладываем сплен 4мм (или Акцент)
- Далее изолируем двери снаружи
- В этом варианте необходимо полностью проклеить все технологические отверстия, и сделать объем двери практически герметичны, в которых будет играть динамик
- Однако сливные отверстия стоит оставить открытыми, чтобы в дверях не скапливался конденсат.
- Обклеить снаружи вибропластом класса Сильвер и поверх него акцентом или спленом
- Следующий этап — шумоизоляция дверных карт, чтобы они не издавали скрипов и других лишних звуков.
- Здесь пригодится антискрипный материал «Битопласт»
- В этой зоне чем толще слой, тем лучше.
- «Сверчки» внутри дверей и оклейка тяг и ручек выполняются с помощью маделина — это антискрип
- Задние двери обрабатываются как передние
- Если в них нет динамиков, то количество слоев уменьшается, а тип материала выбирается тоньше.
Перейти на крышу
Итак:
- Делаем шумоизоляцию крыши для снижения постороннего шума от дождя, исключения его вибрации, а также для удаления «сверчков»:
- Вы уже поняли, как обклеить машину шумоизоляцией
- После поклейки потолка эффект в дождь просто потрясающий — даже в проливной дождь внутри салона остаются только приглушенные удары, которые практически незаметны и не доставляют дискомфорта
- Здесь можно использовать вибропласт Сильвер, вес важен , чем выше вес кровли, тем больше будет смещаться центр тяжести, рекомендуем использовать акцент в 4 или 8 миллиметров, даже в два слоя
- Возможности ограничены, чтобы можно было переустановить обшивку потолка без помех
Днище автомобиля
Шумоизоляция днища делается для уменьшения шума от дорожного покрытия, и от ударов камешков по днищу автомобиля:
- Здесь можно использовать лучшие виброгасители и с хорошими слоями, внахлест, просто не приклеивайте крепеж, иначе будут проблемы при сборке салона
- Топ опять Акцент, лучше небольшой толщины, но в два слоя, здесь чем шире площадь покрытия, тем лучше эффект
- Пристальное внимание нужно уделить места колесных арок внутри салона лучше проклеить потолще (в два-три слоя), в качестве виброизолятора использовать «бимастовые бомбочки», при его отсутствии вибропласт голд
Багажник и колесные арки
В районе багажника много шумов и скрипов, так что не пропустите:
- Особое внимание следует уделить нише запасного колеса, по возможности, полностью оклеен виброизоляционным материалом
- Второй слой Акцент Шумопоглотитель
- Все обшивки в багажнике должны быть проклеены антискрипным материалом «Битопласт»
- Шумоизоляция колесных арок необходима для повышения комфорта в салоне
Инструкция по действию для шумоизоляции колесных ниш снаружи:
- Снять колеса
- Снять пластиковые подкрылки (их нельзя выбрасывать, они служат хорошим звукоизолятором)
- Затем очистить от грязи и клея виброизоляционный материал на поверхность арки, желательно «вибропласт класса Голд»
- В идеале применить «жидкую» шумоизоляцию типа «Ноксидол», она легче наносится и работает лучше и вес меньше и отличная антикоррозийная защита, вместе с арками, днище можно обрабатывать и снаружи
- Если хорошо выполнить работу, то ударов камушков не должно быть слышно вообще.
- Строительная шумоизоляция применяется, как правило, вне помещений , так внутри салона может быть токсичен, в моторном отсеке может гореть или плавиться, а эффект от него может не оправдать ожиданий
- Войлок, даже акустический, подходит в машину с большой натяжкой, т.к. впитывает влагу сам по себе вытягивает его из воздуха, поэтому кузов автомобиля быстро заржавеет, то войлок удовольствие отнюдь не дешевое
- Для использования войлока в автомобиле он должен быть запаян в полиэтилен
- Речь не идет о использование других «альтернативных» материалов вообще
Так шумоизолируются все подкрылки.
Чем можно заменить шумоизоляцию в автомобиле?
Отличный вопрос, стоит только задать его местным «умельцам» и вам дадут кучу советов от строительной шумоизоляции до линолеума с войлоком:
На этом у меня все, дополнительно смотрите видео по вашей конкретной модели.
Значительное количество внешних шумов проникает в салон через двери. Именно после шумоизоляции дверей автомобиля наблюдается заметное снижение внешнего шума. Кроме того, всегда есть возможность полностью «промыть» двери своими руками. Здесь нет сверхъестественных сложностей.
Перед звукоизоляцией — разборка двери
Первый этап — это полная разборка двери, а именно снятие внешней обшивки.Этот этап самый сложный, но не самый сложный. Необходимо запомнить (а лучше записать), какой шуруп или шуруп в каком отверстии был, чтобы тем самым облегчить обратную сборку двери. Механизм открывания и закрывания двери, а также устройство стеклоподъемника можно оставить включенными, потому что поставить их обратно крайне сложно. Эти блоки не будут препятствовать самоизоляции дверей.
Вторым этапом является очистка металла двери от заводской шумоизоляции и ближней к внешней стороне стенки двери — от заводской антикоррозийной обработки.Важно, чтобы поверхность была чистой и обезжиренной – в этом поможет уайт-спирит. Главное не поцарапать краску во избежание коррозии.
Приступаем к звукоизоляции двери
Далее внутреннюю сторону двери (со стороны дороги) следует обклеить вибропоглощающим материалом. Лучше всего подходит Вибропласт Голд, при этом нужно стараться проклеить максимальную площадь, которую позволят технические отверстия в двери. Ползать там не очень удобно, поэтому, чтобы не поцарапать руки об острые края технических отверстий, лучше работать в хлопчатобумажных перчатках.Усиление двери не нужно оклеивать. В настоящее время Aero и AeroPlus от STP все чаще используются для виброизоляции дверного металла. Они легче, чем Вибропласт Голд, что положительно скажется на ресурсе дверных петель. Высокий КМП сделает дверь «деревянной» на стук, двери будут закрываться как у автомобиля более высокого класса с приятным звуком «чпок» вместо «бдзын». Кроме того, новая линейка Aero имеет расширенный температурный диапазон, что особенно актуально для холодного времени года.
Напротив динамика рекомендуется наклеить круг Битопласт, чтобы динамик лучше играл и на него не действовали отраженные от двери звуковые волны. Не обязательно проклеивать Битопластом всю поверхность, потому что этот материал впитывает влагу, а растворение сырости внутри двери – первый шаг к коррозии. Второй слой поверх виброизоляции раньше оклеивал Спланом для тишины, так как обычный Акцент не справлялся с влагой, которая появляется в двери во время дождя.Кроме того, на некоторых автомобилях Splen 8 мм не выдерживали условий эксплуатации и банально отклеивались из-за не водостойкого клея. Теперь доступен материал нового поколения – Акцент Премиум, который абсолютно не боится воды: снаружи покрыт черной пленкой, а с обратной стороны используется влагостойкий клеевой слой зеленого цвета. Поэтому внутреннюю часть двери можно смело оклеивать Премиум Акцентом.
Для меломанов нежелательно использование любого материала (кроме виброизоляции) внутри двери, так как это приведет к появлению неприятных эхо и ухудшению качества музыки.
Если качество звучания акустики не важно, то всю внутреннюю поверхность двери следует оклеить Акцент Премиум или Сплан на мастичной основе. Она должна быть склеена как можно большими кусками, в идеале – цельным куском. Станет тише.
Виброизоляция всех дверных проемов
Проходим к внутренней стороне двери — ближайшей к салону. Здесь есть две возможности.
Если автомобиль готовится к установке мощной акустики, а от установленных в дверях мидбасов ожидается сочная игра, то необходимо закрыть технологический проем в двери плотным и твердым материалом.В зависимости от размеров отверстий для этого может быть использован листовой алюминий или плотный стеклохолст, который затем оклеивается мощным виброгасителем, например, Bimast Bomb Premium или Visomat. Это важно для улучшения качества звучания музыки — из двери должно выходить что-то вроде плотной закрытой коробки. При этом важно проверить работоспособность механизма открывания дверей и стеклоподъемника – чтобы ничего не мешало. Использование Бимаста при уплотнении технологических окон позволяет значительно увеличить массу двери, приходится выбирать: либо петли, либо музыка.
Если качество звука акустики не важно, то технологические окна закрываются гидроизоляцией: важно, чтобы в салон не попадала влага. Для этого подходит STP Aero: легкий и прочный на разрыв. Слишком сильно клеить виброизоляцию не стоит, т. к. увеличивается масса двери и петли могут не выдерживать больших нагрузок.
Есть и компромиссный вариант, применимый для шумоизоляции дверей гражданских автомобилей: технологические проемы закрываем пленкой СТП ВИЭК, а затем на нее накатываем Aero Plus.Таким образом, мы получаем достаточную жесткость для акустики средней мощности, отличную гидроизоляцию и малую прибавку в весе.
Затем следует оклеить эту дверную поверхность материалом Акцент или Акцент Премиум, в крайнем случае — Битопластом 10 мм, сделав необходимые прорези под все механизмы. Участок, близкий к 100%, следует оклеить, оставив место для проводов (если установлен электростеклоподъемник) и динамика.
Звукоизоляционная обшивка двери
Закончив с дверью, приступаем к ее обшивке.На поверхность обшивки рекомендуется наклеить несколько штук виброгасителя (достаточно STP Aero или Vibroplast Silver), чтобы снизить вибрации обшивки. Особое внимание следует уделить стыкам в пластике. Затем вся поверхность обшивки оклеивается материалом Бипласт 10К с запасом по краям в несколько сантиметров. После разрезания битопласта по контуру обшивки он выступит в роли антискрипа – исчезнут все стуки обшивки о саму дверь.Возможен и другой вариант: в местах прилегания обшивки к металлу двери к обшивке по ее периметру приклеиваются планки Мадлен, а изнутри обшивка заполняется Бипластом.
На этом шумоизоляция дверей автомобиля своими руками закончена, можно приступать к установке обшивки обратно. На разных автомобилях дверь разбирается по-разному, но принцип везде одинаков. При звукоизоляции дверей лучше вообще отказаться от Сплина, так как внутри двери от него одни минусы (ухудшается качество звучания акустики, может отвалиться от влаги), а снаружи (между слоями Битопласта) может мешать сборке.
В результате «шум» дверей в машине станет заметно тише, а двери будут легче закрываться за счет увеличения массы.
Шумоизоляция двери автомобиля является основным этапом, если владелец хочет сделать меньше шума и вибраций в салоне. Это связано с тем, что площадь всех дверей велика по отношению к другим частям кузова. Звукоизоляция дверей осуществляется в несколько этапов. Это не слишком сложный процесс. Автолюбитель может сделать это самостоятельно.Строительный рынок предлагает большой выбор необходимых материалов. Затраты на шумоизоляцию не чрезмерны, но понесенные затраты повысят комфорт в поездке и продлят срок эксплуатации автомобиля.
Двери вагона изготовлены из тонкого металла. На скорости при быстром движении они вибрируют от воздушных потоков, вибрируют при неровностях дороги, резонируют при включении акустических систем. Тонкий металл позволяет звукам от проезжающих мимо автомобилей проникать внутрь автомобиля или рядом с ним.Шум от вождения также создается различными элементами самого автомобиля, которые вибрируют при движении автомобиля:
- двигатель;
- коробка передач;
- подвески;
- выхлопные механизмы; шасси
- ;
- уплотнители дверей.
Этот тип шума называется «структурным». Его значение зависит от типа конструкции автомобиля.
Для чего нужна шумоизоляция?
В автомобилях дорогих марок проблема изоляции от посторонних звуков решается производителем.Более дешевые модели имеют минимальную защиту.
Вождение требует максимального внимания, стресса, быстрой реакции на постоянно меняющуюся ситуацию на дороге. Посторонние звуки вызывают дополнительную усталость, притупление реакций, что может привести к дорожно-транспортному происшествию. Акустические динамики часто устанавливаются на дверях автомобиля. Их дребезжание ухудшает качество прослушиваемой музыки.
От шумоизоляции автомобиля ожидается следующий эффект:
- Снижение посторонних шумов.
- Более тихое закрывание дверей. Это следствие увеличения их массы.
- Улучшение звучания установленных аудиосистем.
Дополнительным бонусом является лучшее поддержание комфортной температуры.
Самоизоляция
Правильная шумоизоляция двери на авто своими руками зависит от цели данной операции. Исходя из этого есть четыре варианта:
- Минимум. Решает проблему снижения посторонних звуков, доносящихся с улицы.Он самый бюджетный. Материал приклеивается к внешней стороне двери.
- Среднее. Оптимальный вариант, недорогой и достаточно качественный. Помимо снижения уличного шума, позволяет установить акустическую систему в дверь автомобиля.
- Максимум. Используется при планировании установки акустической системы с усилителем.
- Экстрим. Предназначен для случая, когда в дверях установлена мощная акустика.
Каждый из этих вариантов можно сделать самостоятельно.Выбор также зависит от финансовых возможностей автомобилиста.
Выбор материалов для шумо- и виброизоляции
При выборе материалов для шумоизоляции необходимо обращать внимание на их технические характеристики. Все материалы делятся на следующие основные группы:
- Виброгасители.
- Шумоизоляторы.
- Звукопоглотители.
- Антискрип.
Препарат звукоизоляционный
Виброгасящие материалы битумные, мастичные и комбинированные.Основным показателем их эффективности является коэффициент механических потерь (КФ). Наиболее подходящими материалами являются те, у которых диапазон ПТР составляет 0,8-0,9. Шумоизоляторы укладываются поверх виброгасителей. Звукопоглотители имеют высокопористую структуру. Коэффициент поглощения ими звуковых волн может достигать 95%. Антискрипы уменьшают шумы, издаваемые деталями машины.
Когда автомобилист решит самостоятельно выполнить шумоизоляцию дверей, рекомендуется использовать следующие материалы:
- Вибропласт Серебряный.Это самоклеящаяся алюминиевая фольга. Преимуществом является устойчивость к нежелательной влаге, механическим воздействиям и коррозии.
- Вибропласт Золото. Имеет улучшенные характеристики.
- Бимаст Бомба Премиум. Имеет самый высокий КМП среди битумно-мастичных материалов.
- Селезенка. Устойчив к перепадам температур и погодным условиям. Современная альтернатива – Accent Premium, специально разработанная для изоляции дверей от вибрации и шума.
Этот список не является исчерпывающим.Есть возможность купить комплект для шумоизоляции дверей автомобиля.
Обучение
Перед началом осуществления процесса звуко- и виброизоляции необходимо приобрести следующие материалы и инструменты:
- отвертки, необходимые для разборки дверей;
- ножницы по металлу;
- строительный фен;
- сшивающий валик; обезжириватель
- ; Материалы
- для вибро- и шумоизоляции.
Отвертки понадобятся для первого этапа — разборки дверей.Снимите обивку, чтобы получить доступ к салону. При откручивании крепежных винтов сложно вспомнить, какой из них был в том или ином отверстии, что вызовет трудности при сборке. Рекомендуется использовать ленту, которой следует закрепить выкрученные винты вокруг их отверстий. Разборка стеклоподъемника и механизма открывания не требуется. Эти элементы не будут мешать процессу звукоизоляции.
Процедура установки материалов
Установка шумоизоляции
Как правильно утеплить двери вашего автомобиля зависит от выбранного вами варианта.При стандартной обработке первым шагом является разборка двери. Чтобы получить доступ к существующим поверхностям, снимите обшивку и защитную пленку, если она имеется. Процесс осуществляется в два этапа:
- Обработка внутренних поверхностей салона.
- Обработка поверхностей, обращенных наружу.
Перед началом процесса звукоизоляции поверхности необходимо обработать специальным составом с целью обезжиривания. Следует проверить отсутствие следов жира, ржавчины, грязи.При очистке следите, чтобы краска автомобиля не поцарапалась, иначе со временем в этом месте может появиться коррозия. Работать необходимо в перчатках, чтобы не порезаться об имеющиеся острые углы деталей.
При звукоизоляции внутренних поверхностей для лучшего звучания акустики необходимо закрыть имеющиеся отверстия. Для больших размеров используется стеклопластик или листовой алюминий. Затем наклеивается первый слой виброизоляционного материала. Предварительно прогрейте лист строительным феном.После приклеивания нужно прикатать монтажным валиком. Клеить материал горизонтальными полосами рекомендуется внахлест. Следующий этап – нанесение звукоизоляционного слоя. Затем утепляют наружную поверхность двери. При выполнении процесса важно не нарушать электропроводку, кабели и другие элементы.
После сборки дверей необходимо протестировать результаты своей работы.
Правильная шумоизоляция помогает уменьшить посторонние звуки в салоне автомобиля.Процесс не сложный, можно сделать своими руками.
Как клеить вибропласт — Ремонт и обслуживание 2022
Довольно часто автовладельцы делают шумоизоляцию своих железных коней. Для этого в большинстве случаев используют вибропласт. Этот материал обладает хорошими звукоизоляционными качествами.
Вам понадобится
- — вибропласт;
- — ролик;
- — строительный фен;
- — клей.
Руководство по эксплуатации
1
Сначала отстегните обшивку двери.Также необходимо снять трос ручки и провода, идущие к окну. Теперь перед вами готовая дверь, на которую можно нанести шумопоглощающие материалы. Снимите пластиковую пленку, предоставленную производителем.
2
Далее обезжириваем поверхность двери. Разрежьте вибропласт на кусочки и склейте их изнутри. Нет необходимости оклеивать всю внутреннюю поверхность. Плотно прикатайте материал к поверхности двери. В противном случае он будет работать некорректно, а при нагревании может отвалиться.Чтобы его раскатать, используйте специальный валик.
3
После того, как вы сделали внутренний слой, приступайте к герметизации заводских крепежных отверстий. В результате должен получиться акустический динамик замкнутого объема. Помимо шумоизоляции должно улучшиться звучание динамиков. Вибропласт также можно использовать для герметизации монтажных отверстий.
4
Используя бумагу и карандаш, сначала сделайте выкройки. На них можно вырезать даже детали из вибропласта. Детали должны быть на несколько сантиметров больше самих отверстий.В этом случае материал можно будет прочно приклеить к двери. При необходимости проклейте всю дверь. Помните, что это будет иметь большой вес. При наклеивании материала используйте строительный фен. Нагрейте материал и ровно разгладьте его по поверхности.
5
Аналогичным образом сделать шумоизоляцию всех дверей автомобиля. При необходимости прокладывайте акустические провода сразу. В тех местах, где наличники прилегают к дверям, приклейте вибропласт. Нарежьте его тонкими полосками. Сделайте их шириной примерно 2-3 см.Вибропласт должен быть во всех местах контакта. Соберите дверь в обратном порядке. При необходимости замените неподходящие зажимы на обивке двери.
Днище ВАЗ-2110: ремонт. рекомендации и фото
ВАЗ-2110 — очень дешевый и простой в обслуживании автомобиль. Но одна из главных его «болячек» — это кузов. К сожалению, он плохо защищен от коррозии. Уже после двух лет эксплуатации на нем образуются «жучки». Если игнорировать проблему дальше, останутся сквозные дыры.Ржавчина образуется везде: на арках, крыльях, внизу двери. Но самое уязвимое место в ВАЗ-2110 — днище. Фото и описание процесса его ремонта смотрите далее в статье.
Причины коррозии
Производитель не уделяет должного внимания антикоррозийной обработке этих машин (как и шумоизоляции). Об этом свидетельствуют многочисленные отзывы владельцев. Но если с шумом в салоне еще можно мириться, то дырок в полу нет.
Это неудобно и небезопасно. Соответственно встает вопрос о ремонте или замене днища ВАЗ-2110. Специалисты выделяют несколько факторов, значительно ускоряющих его износ:
- Погода. Металл будет ржаветь при любом контакте с водой, даже если он был окрашен и обработан на заводе. Но дождь – не самый разрушительный фактор. Более агрессивными по отношению к металлу являются солевые реагенты, которыми зимой посыпают асфальт наши дорожные службы.Если часто не мыть дно машины под высоким давлением, соль останется в самых потайных местах. Далее на этих участках будет образовываться ржавчина, а через год – сквозные отверстия.
- Авария. Даже при незначительном ДТП базовый слой эмали и грунт отделяется от металла. Если покраску выполняли неквалифицированные мастера, через 1-1,5 года на том же месте образуются ржавые следы. Такие же возникают, если поверхность была плохо подготовлена к покраске и плохо очищена.
- Забит дренаж. Часто ремонт днища ВАЗ-2110 требуется из-за забитых дренажных отверстий. В итоге вода попадает в салон и багажник. Деваться ей некуда — она поглощена фабричным ковром и мягким шумоизоляционным материалом. Помимо коррозии, он может вызывать характерный запах плесени и гнили. Вода также образуется при использовании негерметичных матов. Текстиль сейчас очень популярен. Но не каждая модель удерживает влагу, из-за чего она впитывается в ковер, а затем уходит на металл.
Таким образом, днище ВАЗ-2110 подвергается негативному воздействию с обеих сторон. Кроме того, очень сложно найти источник проблемы. Не у всех в гараже есть дырка, и никто не будет разбирать салон, чтобы выявить «жучки». Езжайте, пока пол не станет мягким, как желе.
Инструменты
Для успешного ремонта днища ВАЗ-2110 своими руками нам понадобится сварочный аппарат и маска. Электроды не подойдут: металл очень тонкий, и есть риск его прожечь.Поэтому используется только полуавтомат и сварочная проволока. Также нам понадобится болгарка (желательно небольшого размера) и круг для резки металла. Среди прочих материалов следует подготовить листы наждачной бумаги (или соответствующую насадку для сверления), грунтовку, краску, антикоррозийный состав, преобразователь ржавчины. По окончании процесса ремонта днище ВАЗ-2110 нужно будет «зашумить». Но использовать старый материал бесполезно. Поэтому покупаем новые листы вибропласта (лучше 3 мм) и приклеиваем на восстанавливаемую поверхность.
Приступаем к работе. Обучение
Итак, сначала нам нужно подготовить машину. Загоняем его в гараж и разбираем салон. Желательно, чтобы помещение было со смотровой ямой. В зависимости от масштаба работ нам потребуется снять одно или несколько сидений, а также часть коврового покрытия, которое идет на десятку с завода.
На следующем этапе болгаркой вырезаем гнилые части пола. Режем и тот металл, толщина которого меньше заводского — после ремонта он может снова заржаветь.
Обратите внимание, что под днищем проходят топливные и тормозные трубки, а также выхлопная система.
А под задним диваном спрятан бак. Если предстоит капитальный ремонт, все эти элементы следует демонтировать.
Далее тщательно зачищаем все швы наждачной бумагой. Можно использовать специальную насадку на дрель. Оставшиеся следы ржавчины обрабатываются преобразователем цинка. Осторожно: он очень агрессивен. Поэтому работаем исключительно в защитных перчатках.
Если масштаб работ очень велик и для восстановления днища ВАЗ-2110 пришлось вырезать почти весь элемент, важно обеспечить жесткость кузова. В дверные проемы устанавливаем распорки из дерева.
Сварочные работы
Перепарка днища ВАЗ-2110 начинается с обесточивания бортовой сети. Необходимо отключить обе клеммы с аккумулятором, иначе можно спалить компьютер и другие важные узлы. Далее подключаем «массу» сварочного аппарата к кузову и приступаем к работе.
Можно использовать заплатки соответствующего размера или приобрести готовые части пола (особенно это касается порогов). Сварка днища ВАЗ-2110 для восстановления:
- Панели пола.
- Поперек.
- Поддержка сайтов.
- Удлинители лонжеронов и порогов.
- Соединители.
Все новые листы аккуратно захватываются снизу. Шов должен быть не сплошным, а с шагом 5-6 сантиметров.Периодически проверяйте геометрию кузова. Если не учесть этот момент, после ремонта можно получить разблокированные двери. В конце шов можно сделать уже цельным.
Но на этом ремонт днища ВАЗ-2110 не заканчивается.
Отделка
После сварки шов зачищают от окалины. Это можно сделать молотком с зубилом или наждачной бумагой (что значительно дольше). Если шов плохой, переварите участок еще раз. Далее зачищаем металл до блеска и проводим антикоррозийную обработку.А чтобы внутрь не попала вода, используйте герметик. Герметиками обработайте все швы на заплате.
Что дальше?
№Затем нанесите грунтовку и покрасьте. С обеих сторон металл обработать битумной мастикой или пушечным жиром. Благодаря своей жирной консистенции эти составы будут отталкивать воду и не давать ей проникать внутрь к металлу.
Дополнительно можно нанести антигравийное покрытие (если металл обработан мастикой, а не салом). После высыхания сделать внутреннюю звукоизоляцию.Листы с вибропластом следует укладывать на чистую поверхность. На грязи он не держится. А вот на липкой мастике будет держаться в полной мере. Дополнительно прокатываем лист специальным валиком или руками через тряпку. Затем можно смело собирать салон и ставить сиденье.
Как продлить срок службы днища?
Эти советы подойдут тем, кто уже ремонтировал пол на «десятке», и тем, у кого еще есть живой экземпляр. Итак, первое правило – частое мытье.Обычно автовладельцы обращают внимание на верхнюю часть кузова. Но также необходимо промыть его скрытые полости. Особенно это касается тех, кто живет в крупных городах и эксплуатирует автомобиль зимой. Соль никуда не исчезает, пока не будет удалена мощной струей воды.
Следующее правило – регулярная обработка дна. Со временем старый антикор вымывается и отслаивается. Раз в год необходимо проверять его состояние и при необходимости обновлять слой.Если коррозия уже появилась на поверхности (но не сквозной), обрабатываем преобразователем, а затем толстым слоем мастики. Что касается порогов, то они имеют дренажные отверстия. Обрабатывать их снаружи антикором нет смысла — вода внутри. Поэтому в сухую и теплую погоду берем баллончик Мовиля и через тонкую трубочку (она обычно идет в комплекте) заливаем внутрь. Через год эту процедуру следует повторить. Только так можно обеспечить днищу и порогам полную защиту от ржавчины.Если проблема застала вас зимой, можно применить временную меру – зачистить ржавую поверхность и нанести на место антикор местно. А с утеплением сделать обработку по периметру.
Заключение
Итак, мы разобрались, как отремонтировать днище ВАЗ-2110 в гараже. Работа может выполняться в одиночку. Главное использовать полуавтоматический инвертор и не забывать о мерах защиты (маска, перчатки). Если работа ведется впервые, потренируйтесь сначала на ненужных кусках металла.При сварке важно обеспечить максимально ровный и равномерный шов.
Контроль промышленного шума | Промышленная звукоизоляция
Продукция для контроля промышленного шума, которая имеет значение. Повысьте свою производительность и избавьтесь от шума с помощью наших продуктов.
Одной из самых больших проблем, с которыми сталкиваются промышленность и производство, является поддержание приемлемого уровня шума. Шумовое загрязнение – серьезная проблема, встречающаяся в различных отраслях промышленности.Привыкнуть к более высокому уровню шума очень сложно, особенно когда он может влиять на здоровье ваших сотрудников на бессознательном уровне.
Длительное воздействие повышенного уровня шума приводит к усилению стресса, бессоннице и другим серьезным заболеваниям. Это не способ оценить ваших сотрудников, которые являются ключом к вашей миссии и видению. Шум от оборудования может быть подавляющим, почти оглушающим, что является серьезным препятствием для поддержания оптимального уровня производительности.
Наши промышленные звукоизоляционные материалы созданы с учетом этого. Для людей, которые ежедневно сталкиваются с трудными задачами, пришло время создать новую инновационную среду для вас и ваших коллег.
Контроль промышленного шума и акустика
Поддержание уровня шума в допустимом диапазоне стандартных уровней шума OSHA является решающим фактором для здоровья и общего самочувствия ваших сотрудников.
Мы предлагаем различные продукты для промышленной акустики, специально разработанные для уменьшения передачи звука и подавления шума, чтобы идеально вписаться в любую среду.
Acoustical Surfaces — компания, занимающаяся промышленной акустикой, которая предлагает звукоизоляционные материалы для всех отраслей промышленности. Наша продукция универсальна и может соответствовать любой форме и размеру вашего промышленного объекта.
Промышленная звукоизоляция
Наши продукты для промышленной звукоизоляции доступны в виде промышленных стеновых панелей, потолочных плит, ограждений, барьеров и архитектурных элементов. Изделия для шумоизоляции изготавливаются из полипропилена, композитного хлопкового волокна, винила или целлюлозы.Они гипоаллергенны и не слишком сложны в уходе.
С нашей продукцией вы можете быть уверены, что уровень шума значительно снизится. Некоторые из положительных сторон наших продуктов заключаются в том, что все они обладают высокоэффективными изоляционными свойствами и имеют впечатляющую огнестойкость. Используя наши продукты, вы повысите производительность на своем предприятии, обеспечите дополнительную безопасность на рабочем месте и снизите счета. Это отличная долгосрочная инвестиция для вашего бизнеса.
Варианты промышленной звукоизоляции
Благодаря такому широкому выбору опций легко создать эффективное решение промышленной акустики для решения самой сложной проблемы шума. Мы можем создать иммерсивную среду, в которой ваш сотрудник будет чувствовать себя довольным и мотивированным, чтобы достичь максимума в работе.
Звукоизоляция для заводов
Независимо от того, возникают ли проблемы с шумом внутри завода или снаружи, у нас есть идеальное решение для улучшения условий труда. Наша продукция является защитным барьером, который будет защищать ваших работников долгие годы.